Job costing and process costing are accounting and time-tracking methods that have traditionally been used in fields like construction and manufacturing to accurately determine the respective costs of materials, overhead, and labor for either discrete jobs/projects or consistent production processes. More recently, job costing has been adopted by a much wider range of businesses, including consulting firms, advertising agencies, engineering offices, retailers, transportation providers, health care organizations, and others who hope to capitalize on its cost-saving benefits.
Job Costing Defined
Let’s say you’re a business whose projects frequently vary in scope, timeline, or workforce configuration. Invariably, you’ll experience some project-by-project fluctuations in terms of who is working for you, in what capacity, and for how long; and that’s without opening any related “cans of worms” related to materials, overhead, outside consultation fees, or other considerations specific to your industry.
The demand to properly estimate, monitor employee time tracking, bypass unexpected costs, and then deliver on your original estimate to clients while ensuring that your profit margin is sustained in the process; it’s a mighty task. Compound that single project challenge by the number of unique projects you pursue each quarter and it’s an even taller order. The bottom line? Commonly, without job tracking, inefficiencies are undetected, estimate-invoice discrepancies persist, profit margin targets are missed, and finance staff (and general staff) feel overwhelmed by disorganization inaccuracies. Above all, you lose the opportunity to accurately track and analyze what is working well. One of the biggest “wins” of job costing is the ability to determine which project types are consistently most profitable and which members of your organization are already working effectively and efficiently.
In cases like this, job costing or “project-based timekeeping” is our recommended time-, labor-, and costs-management method (read: one with myriad benefits designed to improve financial accuracy, labor efficiency, and client satisfaction). We welcome you to learn about this method in greater depth in our recent article, “Why Accurate Job Costing Is So Important.”
Process Costing Defined
But what if your business, for instance, consistently mass produces a single product or a small number of “replicable” products, which limits the amount of variation in your projects? In this case, your business will benefit from an alternative to job costing called process costing.
Simply put, through process costing, you can accurately calculate your costs for all stages of the production process and determine a price per unit. This involves a good deal of data collection regarding cost information at each stage, inventory analysis, and other steps. Additionally, each company must determine their preferred or most appropriate accounting method to calculate costs: standard costing, first-in first-out (FIFO) or a weighted average approach. In the end, by accurately determining your company’s per-unit cost, you’re empowered to price your products to match your preferred profit margin(s) with much greater consistency and predictability.
Beyond improved profit margins (not that you’re underwhelmed with this prospect), there are a range of additional benefits to implementing process costing. For instance, process costing:
- Offers a predictable, standardized approach: A standardized costing method applies to each period of production, which means you can easily analyze how costs change over time and adjust to guarantee your production costs sync with budgeted expenses. You’re also quickly alerted to inefficiencies or production issues should they arise.
- Streamlines production and accounting to offer ever-coveted “peace of mind”: If your company is regularly producing or mass-producing similar items, process costing is the way to go (read: markedly more practical and simplified than job costing in the context of your industry). Bear in mind, process costing can be more time-consuming at the “onboarding” phase when you’re determining equivalent units and costs per stage, but once activated, it’s comparatively smooth sailing.
- Informs adaptation: After closely observing and accounting for costs per stage and profit margin “hits” or “misses,” process costing provides you with all of the insights you’ll need to address problem areas or adapt end-stage pricing to meet your preferred profit margins.
How WorkForce PayHub Can Address Your Process Costing or Job Costing Needs
Although the benefits of process costing and job costing are clear, it’s natural to feel intimidated by the prospect of concretely organizing, implementing, and managing these accounting and time-tracking processes across a range of projects or production cycles.
Whether you’ve decided to consider job costing or process costing based on your company’s needs, we’re here to help you simplify, launch, and manage the process with minimal headaches (and minutiae) and maximum benefits (read: tangible financial results). We offer guidance and support through our Human Capital Management System and our Time and Labor Management System, both of which work seamlessly with job costing and process costing strategies. In sum, we offer the software, personnel, and expertise to make what seems like a dizzying accounting and time-tracking endeavor into a comprehensible and valuable tool for cutting costs and inefficiencies and making life easier and more profitable for your company.
Please contact us today to discuss how we can track your labor and production costs to improve your profit margins and company-wide efficiency.
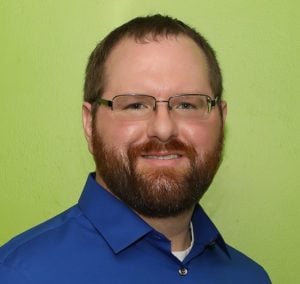